Blog
Choosing the correct insulation for your cable isn’t just about picking a material—it’s about optimizing performance, safety, and longevity. Different insulation types suit various environments and applications, and understanding the properties of each helps you make informed decisions.
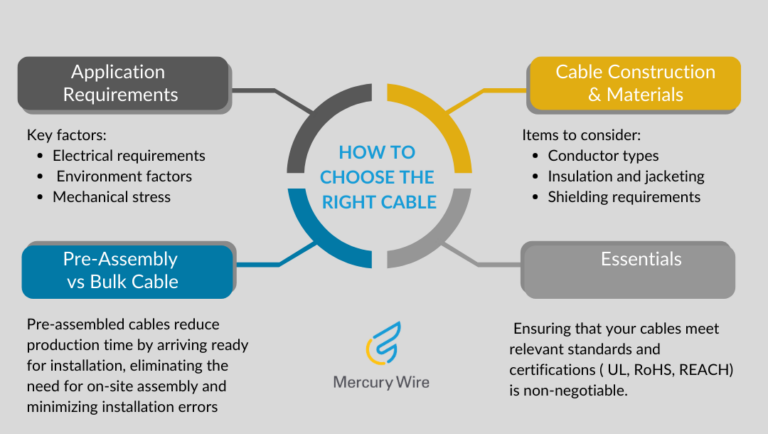
Here’s a guide to some of the most commonly used insulation types and where they shine.
PVC (Polyvinyl Chloride)
Strengths: Flame resistance, UV protection, flexibility.
Best Applications: Commonly used in appliances, medical devices, and outdoor environments, PVC is versatile and cost-effective. Its flame resistance and durability against UV exposure make it suitable for settings with moderate environmental demands. For instance, a medical device that needs flexibility and easy sterilization might incorporate PVC-insulated cables, as the material resists chemical exposure well. Here is a table with the detailed information.
Polyethylene (PE)
Strengths: Moisture resistance, temperature stability, excellent dielectric properties.
Best Applications: Known for its ability to handle high-frequency signals, PE insulation is perfect for data and telecommunications cables. Its moisture-resistant and durable nature makes it ideal for outdoor cables, such as those used in telecommunications networks exposed to fluctuating temperatures. Additionally, PE is commonly found in cable applications within harsh environments that need both high performance and reliability. Here is a table with more information.
Polyurethane (PUR)
Strengths: Abrasion resistance, chemical resilience, flexibility.
Best Applications: PUR insulation is a rugged choice for cables that need to endure tough industrial environments. Often found in the marine and automation industries, PUR insulation can handle consistent wear and tear. Consider a cable used in a factory setting where equipment is frequently moved; PUR insulation offers the durability to resist abrasion and chemical exposure, ensuring long-lasting performance.
Chlorinated Polyethylene (CPE)
Strengths: Oil resistance, flame retardance, UV stability.
Best Applications: CPE insulation is designed for environments that face significant chemical and mechanical demands, such as power plants or construction sites. In these settings, durability against oil, flame, and UV exposure is essential. For example, power cables in an industrial plant might be insulated with CPE to endure intense temperatures and exposure to oils and chemicals without degradation. Here is a more detailed table.
Nylon
Strengths: Abrasion resistance, flexibility, protective layering.
Best Applications: Often layered over other insulation materials, nylon is used to enhance abrasion resistance, making it suitable for applications with high wear and tear, such as automotive wiring. In a setting like automotive manufacturing, where cables are frequently exposed to mechanical stress, nylon provides additional protection to the underlying insulation, ensuring longevity in demanding conditions. Here is more information.
Key Considerations for Choosing Insulation
When selecting insulation, consider the environmental conditions, flexibility needs, safety standards, and lifespan required for your application. Each insulation material offers unique advantages, and balancing these against your needs will lead to the best solution. Mercury Wire offers expert insights into creating custom cable solutions that align with specific industry requirements, so don’t hesitate to reach out for guidance on selecting the best insulation for your cables.
For more detailed insights, visit Mercury Wire’s jacketing and insulation insulation guide. Need more information, why not reach out to one of our specialists who can provide you with guidance based on your specific needs.